Machining subcontractor for over 30 years!
LDPE, a flexible and resistant plastic
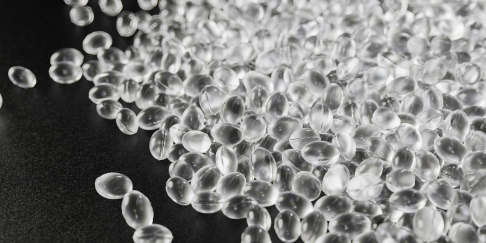
About LDPE
Low-density polyethylene (LDPE) is a plastic known for its flexibility, impact resistance, and excellent chemical tolerance. Widely used in the manufacturing industry, it is valued for its ability to be easily thermoformed and welded. Its low production cost, combined with its technical performance, makes it a preferred choice for many applications, ranging from packaging to the machining of industrial parts.
Need custom LDPE parts?
At 3D Coupe, we are experts in machining technical plastics like LDPE. Whether it’s for high-precision parts or solutions tailored to your industrial needs, our expertise is at your service. Contact us to discuss your project!
LDPE Characteristics
Mechanical Performance
- Flexibility and impact resistance: LDPE effectively absorbs impacts, making it ideal for applications that require some bending without breaking.
- Low density: it is lightweight, reducing the overall weight of manufactured components.
- Good abrasion resistance: it offers increased durability in environments subject to moderate friction.
Thermal Performance
- Operating temperature between -50°C and 80°C: it retains its mechanical properties over a wide temperature range.
- Good moderate heat resistance: although its melting temperature is relatively low (~105-115°C), it remains stable in standard applications.
Chemical Performance
- Excellent chemical resistance: it tolerates diluted acids, alcohols, and various solvents.
- Low water absorption: it does not easily degrade in wet environments, making it ideal for applications in aqueous environments.
Practicality
- Easy to machine: its flexibility and compatibility with machining techniques such as milling and cutting make it a preferred material.
- Good weldability and thermoformability: it is easy to assemble and mold according to specific needs.
- Recyclable: although it is not as reusable as HDPE, it remains an eco-friendly choice for certain applications.
Uses of LDPE
LDPE is widely used in the manufacturing of plastic films, flexible packaging, chemical tanks, insulating sleeves, and industrial components requiring flexibility and chemical resistance. Its affordability and ease of processing make it a strategic choice for several industries.
FAQ and Comparisons
What is the difference between LDPE and HDPE?
LDPE is more flexible and more transparent, while HDPE is more rigid and more resistant to impacts and heat. LDPE is ideal for flexible packaging, whereas HDPE is preferred for rigid containers and structural parts.
Is LDPE UV resistant?
No, it degrades under prolonged exposure to UV, which limits its outdoor use without stabilizing additives.
Can LDPE be welded?
Yes, LDPE can be easily welded using various methods, including hot welding and extrusion.
LDPE vs PVC: which is the better choice for insulating sleeves?
PVC offers better thermal and mechanical resistance, but LDPE is more flexible and chemically inert, making it ideal for certain electrical applications.
Is LDPE a good choice for chemical tanks?
Yes, thanks to its chemical resistance, it is often used to contain various corrosive liquids.
Can LDPE be easily recycled?
LDPE is recyclable, but its recovery is less common than that of HDPE due to the complexity of sorting.
Why choose LDPE over another flexible plastic?
Its excellent value for money, impact resistance, and flexibility make it a wise choice for applications where these properties are essential.
LDPE Machining Specialist
We have the expertise and equipment necessary to transform LDPE according to your needs. Turn to 3D Coupe for custom parts and solutions tailored to your industrial requirements!
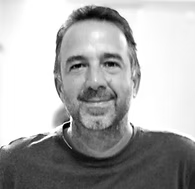
We drive our clients’ growth through smart, customized subcontracting partnerships.