Machining subcontractor for over 30 years!
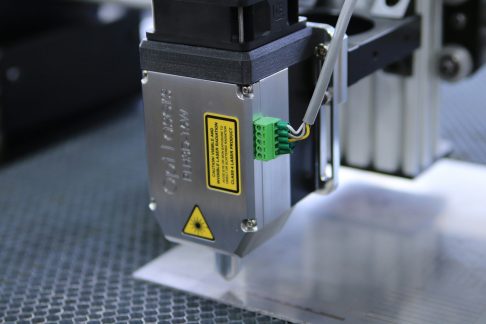
Over 12 areas of expertise under one roof. We can help you achieve your production goals.
5 effective ways to reduce your machining costs
In an increasingly competitive industrial market, optimizing machining costs is a crucial challenge to maintain profitability. Discover how Lean manufacturing and other innovative approaches can transform your production.
The Current Challenges in Industrial Machining
The manufacturing industry is facing major challenges in 2025. Rising raw material prices, increasing energy costs, and international competitive pressure place machining cost reduction at the heart of companies’ concerns. According to recent sector data, machining costs account for between 15% and 30% of total production expenses for most manufacturers.
Plastics machining, in particular, is increasingly in demand as efforts are made to make components lighter in the automotive and aerospace sectors. However, there is a need to optimize the costs of this activity. Companies that fail to control their expenses risk losing their competitive edge in a market with low profit margins. A study conducted with 150 manufacturing companies revealed that those that implemented machining cost optimization strategies improved their profitability by an average of 18% over two years.
The Trends to Watch in Cost Optimization
Accelerated Adoption of Lean Manufacturing
Lean manufacturing remains one of the most effective approaches to reducing machining costs. This methodology, focused on eliminating waste and optimizing workflows, allows companies to identify and remove non-value-added activities in the machining process.
Pioneering companies in applying lean manufacturing to their machining operations have reported cost reductions of up to 25%. The implementation of visual dashboards, regular Kaizen sessions, and the involvement of operational teams in continuous improvement are proven practices.
Digital Transformation in the Machining Workshop
The integration of digital tools is changing the way machining costs are managed. Real-time monitoring systems enhance machine usage and prevent breakdowns through preventive maintenance.
Numerical simulation software also allows for virtual testing of different machining configurations before actual production, reducing costs related to trial and error. A company specialized in plastic machining recently reduced its setup costs by 40% thanks to these technologies.
The Rise of the Circular Economy
The circular economy offers new opportunities to reduce costs. Recovering and recycling machining waste, particularly in metalworking, adds value to what was previously considered waste.
In the field of plastic machining, some innovative companies have developed systems enabling up to 30% recycled material to be reintegrated into their production, generating substantial savings on raw material purchases.
5 Practical Tips to Reduce Your Machining Costs
1. Optimize Part Design from the Start
The design phase accounts for 70% to 80% of the final cost of a machined part. An optimized design for manufacturing can drastically reduce machining costs:
- Simplify geometries to minimize the number of operations and required tools
- Avoid excessively tight tolerances when they are not functionally necessary
- Standardize part features as much as possible
- Consult your machining experts during the design phase to incorporate their constraints
An aerospace company managed to reduce its machining costs by 28% by simply rethinking the architecture of its components to facilitate manufacturing.
2. Adopt a Strategic Approach in Material Selection
Material selection directly impacts machining costs:
- Opt for materials that are easy to machine when technical specifications allow
- For plastic machining, consider polymer grades specifically formulated to facilitate machining
- Assess the total cost of ownership rather than just the material purchase price
- Standardize your material catalog to benefit from economies of scale
3. Implement Lean Manufacturing Principles
Applying lean manufacturing principles systematically eliminates sources of waste:
- Map your value chain to identify non-value-added steps
- Standardize machining processes to reduce variations and errors
- Implement a preventive maintenance system to maximize equipment availability
- Train your operators in continuous improvement techniques
4. Invest in Machining Technology Tailored to Your Needs
Choosing the right machining technologies is crucial for reducing costs. It is important to strike a balance between using traditional machines and automated machining centers, depending on production volumes. It should also be considered that:
- Multi-axis machining can significantly reduce the number of required handling operations.
- The integration of continuous measurement systems allows for quick detection of potential issues.
- The use of advanced programming software optimizes tool movements.
5. Optimize Your Production and Supply Chain Management
Effective production and procurement management significantly contributes to cost reduction:
- Consolidate similar orders to minimize setup and tool change times
- Negotiate framework agreements with your suppliers to obtain better rates
- Implement advanced planning systems to maximize equipment utilization
- Streamline your cutting tool inventory and standardize your tooling catalog
An automotive component machining company reduced its procurement costs by 18% by streamlining its supplier panel and negotiating multi-year agreements.
Cost Optimization: A Priority Project
Machining cost optimization is a standalone project that deserves dedicated attention. Companies must adopt a comprehensive strategy, integrating lean manufacturing and advanced technologies, to remain competitive.
Start by analyzing your current situation to identify the optimal improvements tailored to your business reality.
Do you also want to optimize your machining costs?
Start by developing a subcontracting partnership.
FAQ
What machining services do you offer?
See all services
What materials do you work with?
Plastics, foams, wood, and non-ferrous metals
I want to optimize my production costs
By working transparently and identifying mutually beneficial opportunities, we can build a growth-focused partnership and significantly reduce material and production costs.